My Museum of Plastics: Who’s looking at you?
It feels like plastics are unavoidable in the house and we are all making great steps towards reducing our single use plastics in particular. However there are some items I welcome in to my home and it is still worth celebrating plastics and the incredible utility and design they have brought to society.
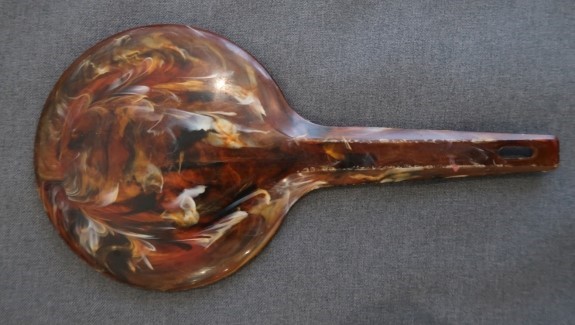
This is a hand mirror I bought from a flea market around 10 years ago. I bought it because I loved (and still love) plastic collectibles and this had a beautiful design and imitation tortoiseshell pattern. It is on ‘open display’ on top of a chest of drawers out of direct sun light with a semi-regular maintenance plan (it’s dusted occasionally). It measures 270 x 140 x 20mm. There are no manufacturer’s labels on the mirror at all and the design doesn’t necessarily point to one particular era. Can I identify what kind of plastic it is made from?
With very limited resources at home there are still a few things I can use to try and identify the type of polymer. First, I carried out some research and found and article on ‘The Characterization of Tortoiseshell and its Imitations’ (Hainschwang & Leggio, 2006) which stated that imitation tortoiseshell was initially made from cellulose nitrate (semi-synthetic) and then from cellulose acetate (semi-synthetic), casein formaldehyde (semi-synthetic), phenol formaldehyde (synthetic) or polyester (synthetic) when the flammability of cellulose nitrate made it unsellable. This gave an indication of the polymer type but I wouldn’t necessarily disregard other types at this point. I don’t think it can be casein as that was mainly used for small items such as buttons and knitting needles, therefore I discount it. I then tried to date the mirror but, due to the popularity of the tortoiseshell appearance, this was hard to determine and could have been from any time from the late 19th century to present day. I guess mine is mid-20th century but that is a pure guess! This left me with more practical identifying techniques.
First the appearance. As I said above there are no identifying or manufacture labels but there are flash lines on the base of the mirror and going all the way around the edge, showing it is a moulded polymer rather than natural tortoiseshell which would be heated and pressed in to shape (phew!). There is also a raised circle on the tip of the handle which would have been part of the mould. The plastic is semi-translucent brown with white and black swirled through it to give the tortoiseshell appearance. Looking closely at the back of the mirror it seems that there are two layers of the polymer which makes up a varied and more ‘natural’ appearance. Cellulose acetate, phenolic resins (such as phenol formaldehyde) and polyester resins are all injection moulded polymers.
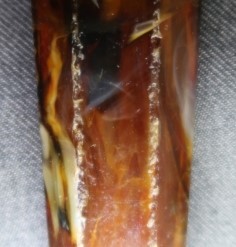
The condition of the object is surface scratching overall giving a dullness to the otherwise high gloss. Also, I can see on the handle that the polymer has started to delaminate highlighting a creamy white colour. As this is where the mirror would be held I would suggest this has been caused by moisture, acids and dirt transferred from the hand. Both polyester resin and cellulose acetate are sensitive to hydrolysis.
At this point I decide to contact the Plastics Historical Society whose members are experts at identifying plastics to see if they can give me any information and pointers. In the mean time I persevere with my ‘at home tests’.
When you work with historic plastics you start to be familiar with the different ‘feels’ of various types, for example plasticised PVC has a flexible and oily surface texture that can be dented by a finger nail. My mirror is fairly light becoming weightier at the mirror end. The surface has a high gloss that has dulled with mechanical wear and tear. It doesn’t feel oily but feels hard and vaguely rough when rubbing the hand over. It cannot be dented by a finger nail which makes me discount PVC. The feel and sound when it is tapped is very ‘plasticky’ which makes me discount phenol formaldehyde (Bakelite) or phenolic resin as this has a more dull sound normally, and is much more dense and heavy then this plastic. Also – I have dropped this mirror many times and it has never cracked or broken whereas phenolics are very brittle.
I start to think that my mirror might be made of either polyester of cellulose acetate and at Tate (where I work), I might then use FTIR to confirm the identification... but... I don’t have that access in lockdown so I turned to smell instead! Some polymers have easily identifiable smells which we can use to pin point the type, for example cellulose acetate smells of vinegar; casein formaldehyde smells of burnt milk and polyester smells of acrylic. Unless the plastic is degrading a smell isn’t normally noticeable from an object, therefore I have to do something to the surface to make it smell. There are three main ways to ‘activate’ the smell – 1. By scratching the surface – 2. Immersing the item in hot water – 3. The hot pin test where I heat a metal pin on an open flame and then apply this to the polymer surface (NB: These are destructive tests and not something I would carry out on the Tate collection!). I tried each test on the handle including the hot pin test where the pin went in to the surface easily with no smoke and sadly no smell! But still I have a few more clues. The hot pin test may not have been completely successful as I might not have been able to get the pin hot enough. Also – I have hay fever at the moment which could have hampered my sense of smell!
While messing around in the kitchen, Colin Williamson had been in touch. He is a polymer specialist and member of the Plastics Historical Society. He has a particular interest in identifying plastics and is happy to help me with my mirror.
CW: ‘My instinct suggests that it is cellulose acetate and made by injection moulding but if I had it in my hands I would first of all look for a point on the rim where all the swirls originate. If there is one to be found (often by touch) then this would support my guess.
The material is transparent in some areas and there are not that many transparent plastics, cellulose acetate (CA), cellulose nitrate (CN), polystyrene, cast phenolic, pmma and polyester are possible but pmma and polyester (PS) would be 1950s at the earliest and the item does have an appearance of 1940s. The circle is a mould mark and suggests injection moulding. CN is not injection moulded and transparent PS has a metallic ring when knocked so these are mentally eliminated.’
With Colin’s incredibly helpful I response I looked at the mirror again and found a slightly raised bump at the tip of the handle which looked like an injection point. This confirmed that the item had been injection moulded. I responded to tell him about my hot pins test and also to ask whether cellulose acetate could have white mixed with it – in my mind I always think of CA being clear or brown. He said that CA can have almost any colour mixed in with it and asked further questions about the hot pin test – ‘you should have a softer surface with CA and easy penetration and acetic acid smell and, dependant on the temp, smoke. Polyester normally smells styrinic and is harder’. The soft surface seemed to tally with my test. He also mentioned that ‘the mould parting line going right round the item would not be probable with polyester, the resin is poured into a two part mould, there would be trapped bubbles…the evidence still points to CA, injection moulded on a plunger machine’.
So I seem to have been able to identify my mirror as cellulose acetate! This is really exciting as it probably means that it is older than I thought and also proves that there are ways to identify plastic objects when we don’t have access to scientific analysis. Of course I will also try to confirm the result when the lockdown is over but in the mean time I have a new appreciation for my mirror.
Many thanks to Colin Williamson for his guidance.